Tips for Bodywork
In order to get your car’s finish looking top notch, the paint needs to have a smooth and damage-free base. For that reason, it’s worth understanding the various steps and techniques to ensure your car’s body panels are in great shape, ready for painting.
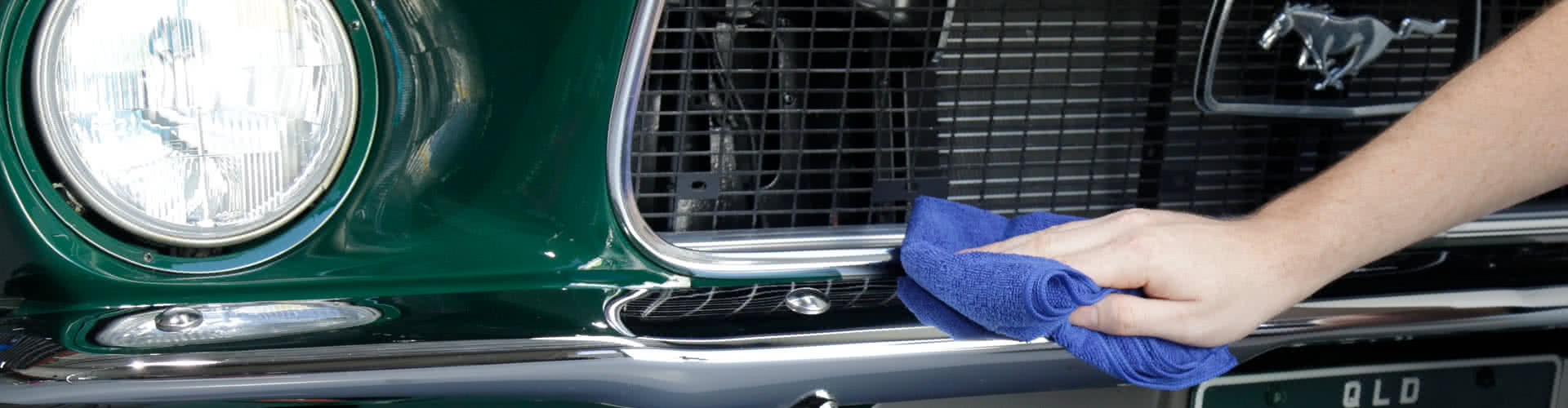
What’s the best way to remove dents?
Whether from stones or other debris that’s thrown up from the road, careless people in the carpark, or a little nudge into something here or there - Dents are almost unavoidable if you use your car frequently. There’s no one perfect solution for fixing dents since the type of repair is necessitated by the level of damage to your panels. Pulling simple dents can be done with relative ease though, and in some cases without the need to even remove paint.
Suction cup style pullers can be used to quickly and cleanly remove small dents, but for creases or compound denting, a bit more intensive bodywork will need to be carried out. To properly deal with more severe dents, usually, the use of panel hammers and dollies is required - to beat the metal back into the right shape. This won’t result in a perfect finish; body filler is applied on top, then sanded down into a smooth and even finish once it’s dry.
Why are cutting and welding panels necessary?
Old cars usually see rust and rot on fenders, doors, quarter panels, boot floors, and interior floor pans. Damage from rust and rot varies, every repair will be a little different from car to car. There are two methods to repair rust on body panels. You can cut out the damaged section and weld in a patch panel, or replace the entire panel.
Most body shops will simply replace the entire panel where possible because it's quicker and more cost-effective. The labour is usually less than it would be to repair the rust, but you pay more for the replacement panel which can be pretty pricey or incredibly hard to find. If there is no collision damage or the panel isn’t easily removable, then the alternative is to cut out the rusted area and weld in a patch panel. Provided you are a decent welder; you can save money and repair rust on body panels yourself.
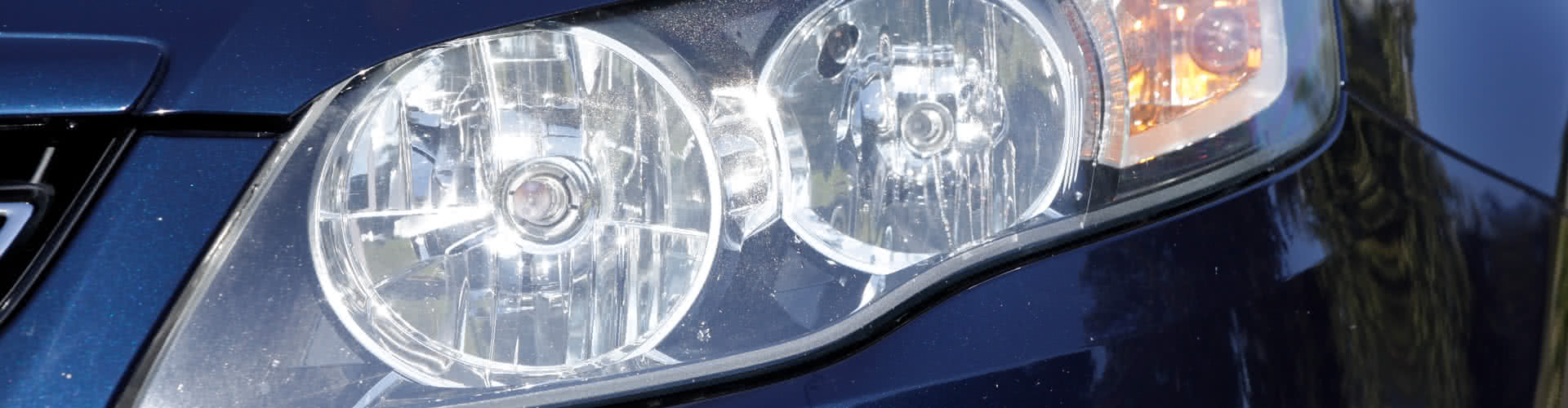
What’s the best way to cut out rust?
Cutting out rusty metal to be repaired can be done in several ways, but before you start grabbing tools, stop and think about the best plan of action. You’ll need to factor in your available space, your budget and the time you want to spend working on it. Having the right tools makes all the difference, providing that you use them correctly - an air compressor and air tools will save you time and allow you to work more effectively, but electric tools are often just as useful. Hand tools are the way bodywork was done back in the day, but it’s pretty inefficient and incredibly difficult to get a good result from tin snips.
Before cutting out any rusted metal, clean off the area. Take a scraper or putty knife and scrape off any loose rust on the body panel to be worked on. Then take masking tape and mark out about one inch around the rusted-through part. You want to remove as little good metal as possible. The big key here is to think it through before cutting.
Use an air sander to quickly bring the rusted area down to bare metal. A 36-grit sanding disc works best. Sand beyond the rusted area an inch or so. Once down to bare metal, all the damage is revealed. Clean the exposed metal area with a 60 or 80-grit disc. You should now have a shiny, solid rust-free surface.
Again, take masking tape and mark off the intended cut area. You can use tin-snips, or a coarse file to remove the rusted metal, but an air-powered cut-off wheel is fastest. Slice along the taped line with the cut-off wheel, letting the air tool do the work. Don't force it to cut faster, as this will overheat the tool and the metal. This will make a lot more work for you. Once the damaged metal is removed, it's easier to see the best way to make the patch.
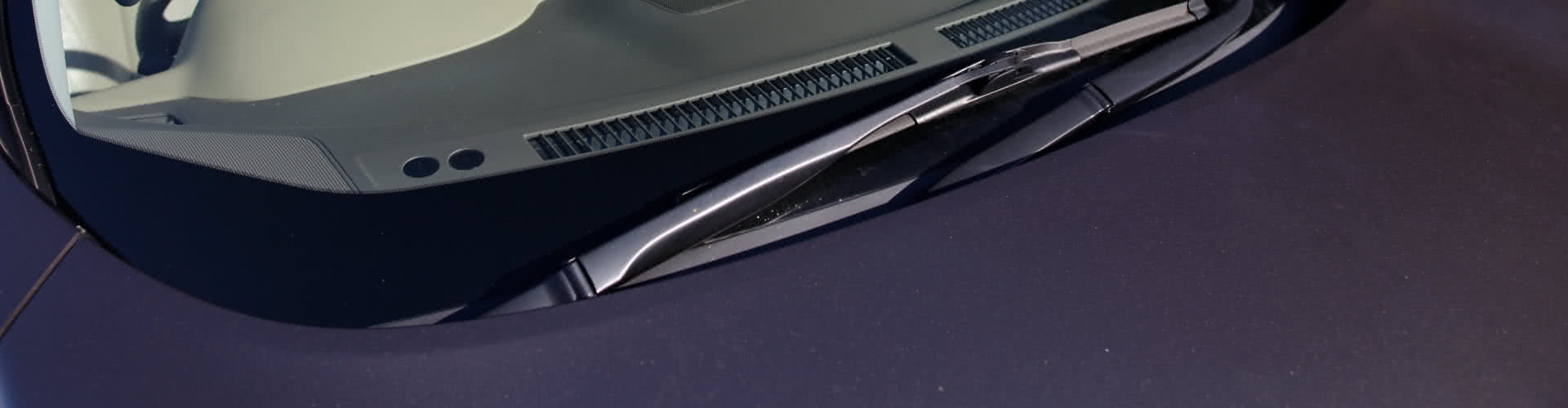
Cardboard Patch Template
After carefully cutting out the rusted metal from the panel, the next step is to make a patch template. Take measurements and transfer them to a piece of cardboard (the kind you can cut with a scissor). Draw out and cut a template of the patch panel needed. Start larger than you need, then trim gradually until a perfect fit is achieved. After that, scribe or mark the cardboard template onto a piece of sheet metal.
How do I cut sheet metal?
If you can't purchase a new piece of sheet metal stock, an old piece of panel from a donor car can be used, as long as it's grinded clean and the same thickness. On older (pre-seventies) American cars and trucks, the width of the original sheet metal is most likely 18 or 20 gauge. Carefully cut out the metal template, checking and re-checking it against the car for an exact fit. You want to end up with a gap of no more than 1/8".
Using hand-held nibblers and tin-snips work fine for smaller patches, but electric shears will save time on larger patches. You can use a black marker to mark the cut, remembering to add about an 1/8th" or so to the line for trimming. Once you have the rough patch cut out, carefully trim it down with hand-held snips.
Patching into a curved area of the car body will take more time and skill and a simple flat patch. Before cutting out the old metal, study the damaged area and think through the repair process. You may decide to remove the entire section to make the patch and welding more accessible. Cutting the panel bigger than the damaged area may give you a cleaner and easier butt weld.
With the panel shaped, test fit it to the car body several times, then clamp it down. Welding new to old rusty metal is always tricky, especially after grinding the rust off old sections, which thins the metal even more. Burning through the old metal is always a worry. The following article covers tips and techniques for welding sheet metal.
*Important information* - Click here to read more about our DIY Advice Terms and Conditions.